Companies that use a modern warehouse management system (WMS) with integrated order processing can, on average, increase productivity by 25%, space usage by 20%, and stock use efficiency by 30%.
This results in more profits per square inch on the floor, getting orders out the door faster, and making it very hard to make a mistake. These are essentials for growing your business, increasing profitability, and meeting increasingly higher consumer standards. To learn more about how we can help you, request a demo of our WMS system today.
Discover why companies trust Deposco when It’s Grow Time™ .

Key Takeaways
- WMS systems boost efficiency, improving stock usage by up to 30%
- Cloud-based WMS offers flexibility and real-time integration capabilities
- End-to-end platforms combining WMS and OMS streamline operations and boost satisfaction
- Most businesses can start achieving ROI within 90 days
- Consider scalability and implementation approach when selecting your WMS
How WMS systems work
A WMS is a warehouse management software solution that uses 100% real-time visibility to optimize and manage the daily operations of a warehouse. This includes inventory tracking, order fulfillment, picking/packing, shipping, and logistics management.
It solves the growing challenge of how to get more orders to the right locations with confidence, speed, and virtually no mistakes – at a lower cost.
WMS systems make your inventory data fully transparent and accessible to all the players involved in fulfilling an order:
- Empower staff to choose the fastest, cheapest pick, pack, and ship method on every order
- Easily see what inventory is available and where it is at all times
- Get AI-driven recommendations to simplify decisions and unlock massive operational efficiencies
- Leverage a flexible technology architecture that offers freedom to add new features faster
- Sell more products in more creative ways
That includes best picking and packing strategies – such as batch, bulk, case/pallet, each, and cartonization. Labor-strapped teams can easily prioritize orders, and even individual items as part of the order, with the ideal collection routes. And ensure all the necessary products ship on time, every time.
Intelligent order routing and inventory allocation can be configured to your specific warehouse managing system and processes, which means more profits per square inch on the floor.
With real-time data being fed into scanners, it’s very easy for staff to get orders out the door fast. And very hard to make a mistake.
Who uses WMS systems?
- Retailers, CPG brands, and ecommerce businesses that struggle with the rising cost of out-of-stocks, overstocks, labor, and rapidly shifting customer preferences use WMS software. It’s the smartest move for companies under pressure to deliver fast, flawless fulfillment experiences at optimal margins.
- Third-party logistics (3PL) companies also use warehouse management systems to streamline and simplify the complex service requirements of an increasingly diverse client base. A 3PL WMS enables same-day onboarding for new clients by providing a structured and efficient framework for integrating their operations. Additionally, the automation capabilities save significant time in billing and escalation processes within a customer portal, allowing the 3PLs to focus on delivering high-quality service. By leveraging a cloud-based WMS with robust integrations, 3PLs offer the most innovative technology solutions to their clients, increasing revenues, reducing operational costs, and minimizing client churn.
Along with a 64% increase in order volume in 3 months and a 25% improvement in cycle count accuracy.

This technological edge ensures that 3PLs remain competitive and responsive to the evolving demands of the logistics industry.
Learn more about 3PL warehouse management solutions.
What size company benefits the most?
Mid-market firms competing in tight markets get the greatest financial gain from warehouse managing systems. Specialty retail and clothing, health and beauty, and 3PL providers are good examples of companies feeling the greatest pinch of logistics costs and labor challenges.
They feel “stuck,” experiencing diluted margins in meeting customer expectations, but lack the internal resources to keep going without innovating. They may not be ready for the high price tag of an enterprise solution, but the manual work and limited functionality of their ERP’s fulfillment modules hinder growth strategies from taking shape.
Mid-market businesses that switch to a modern WMS system create massive efficiencies in storing, picking, packing, shipping, and moving inventory. This alleviates labor problems all while improving revenues and customer experience within 90 days of implementation.
Read more: Customers using Deposco’s WMS have seen a +63% increase in top-line growth and a 150% increase in fulfillment efficiency alongside +99% order and inventory accuracy.
Warehouse software options to consider
When it comes to understanding all the various types of warehouse software for your company, you have many options. The acronyms start to look like Alphabet Soup:
- WMS – Warehouse Management System
- WCS – Warehouse Control System
- WES – Warehouse Execution System
- MRP – Warehouse Material Requirements Planning System
- ERP – Enterprise Resource Planning
- OMS – Order Management System
- TMS – Transportation Management System
The options and different categories can be confusing, and not all are created equal! Some of these acronyms are included in a WMS system. Others are completely different and connect to a WMS. Then, even within WMS systems, the types vary.
Learn more about these types of warehouse software, or keep reading to dive deeper into types of WMS.
Categories within WMS
Warehouse systems range from standalone tools, modern OMS + WMS, and specialized 3PL WMS systems to monolithic supply chain software platforms, ERPs with bolt-on warehouse managing system functionality, and cloud-based or on-premise solutions.
Monolithic or best-in-breed supply chain software
Refers to a suite of digital tools designed to manage and optimize the flow of goods, information, and finances through the supply chain. These monolithic product suites are often developed for large enterprises and come with a hefty price tag, extended implementation times, outsourced support, hidden costs, slow change management, and higher risk. While they boast all the bells and whistles, many may exceed your current needs and cannot be easily customized to meet your unique requirements.
This lack of flexibility hinders operational efficiency and adaptability, making it challenging to respond to dynamic business demands. In the early days of ecommerce, technology acquisition looked very different. Trying to simplify things, companies bought all their supply chain software from a big name. Over the years, the evolution of monolithic product suites has brought substantial risk to businesses seeking frictionless growth.
Avoid the Monolithic Suites Approach!
Best-in-brand isn’t always best. Learn the perils of just going on a name vs. a modern WMS system built on one codebase, by one team, with regular investments in innovation and in YOU.
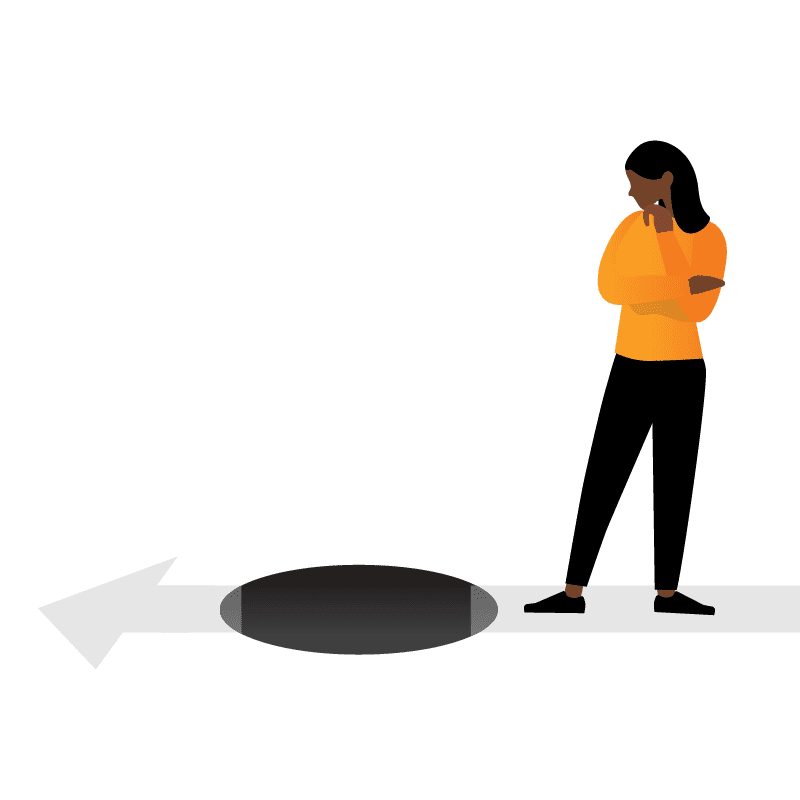
ERP Inventory Fulfillment Module
An Enterprise Resource Planning System (ERP) is a huge category of accounting-first software, typically a suite of modular business applications that an organization can use to collect, store, manage, and interpret data. Inventory fulfillment in ERP is informative, but not directional or timely in terms of optimizing decisions in the warehouse. The main difference between ERP vs. WMS is an ERP reports inventory data as it relates to accounting, but lacks the efficiency and depth of logic that you get from a dedicated WMS.
ERP vs. WMS: What’s the Difference?
Can’t get a handle on orders? Maybe it’s because your staff is busy bouncing between multiple systems, scouring through spreadsheets and papers, piecing together unreliable data points, and handling customer complaints – rather than moving on to the next order. If so… Congrats; you’ve outgrown your ERP. Stop trying to fight back with an accounting-first system that can’t keep up.

On-premise warehouse management systems
An on-premise WMS is a warehouse management system that is installed on local servers and managed internally, making it less adaptable, responsive, and connected compared to cloud-based WMS. On-premise systems require significant time and resources for updates and customizations. Any issues demand support from in-house IT, leading to slower response times. Additionally, integrating on-premise WMS with other supply chain applications is complex and resource-intensive.
Cloud-based warehouse management systems
A cloud-based WMS system is a modern software application built to manage the operations of a warehouse or distribution center. These dedicated systems incorporate mobile devices along with barcodes and RFID scanning/sensing to streamline warehouse operations and workflows, such as:
- Receiving, put-away, stock locating
- Inventory management, cycle counting, task interleaving
- Wave planning and order allocation
- Order picking packing, inventory replenishment, and shipping
- Labor management and performance tracking
- Automated materials handling equipment (MHE) interfaces
Cloud-based WMS solutions offer greater flexibility, faster issue resolution, and easier integration with other critical supply chain applications. They even connect seamlessly to existing ERP or CRM systems, making it a more attractive option for businesses needing to stay agile and competitive.
Advanced systems for warehouse management make extended capabilities readily available as components of the cloud platform. These may include labor management, slotting, yard management, voice picking, parcel manifesting, wearables, AI-based shipping management software, and supply chain automation.
Compared to on-premise, cloud WMS solutions drive greater long-term value through productivity, rapid cost reduction, accuracy and reduction of human error, speed and agility, enterprise visibility, and massive throughput improvements.
Learn more: What is a Cloud-Based WMS and Why Do You Need One?
WMS vs. OMS
What is the difference between a WMS and an OMS? A cloud-based order management system tracks orders, inventory, and customer information in real time within a centralized OMS platform. A warehouse management system is more about managing and optimizing warehouse operations processes including picking, packing, shipping, and receiving.
To confuse things further, flexible WMS systems like Deposco offer an OMS integrated within the same platform and codebase, making business growth seamless. You get several benefits that only emerge when the two are deployed supporting each other.
WMS and OMS Are Better Together
Learn the benefits of a warehouse management system with a seamless, integrated path to order management in the same platform.
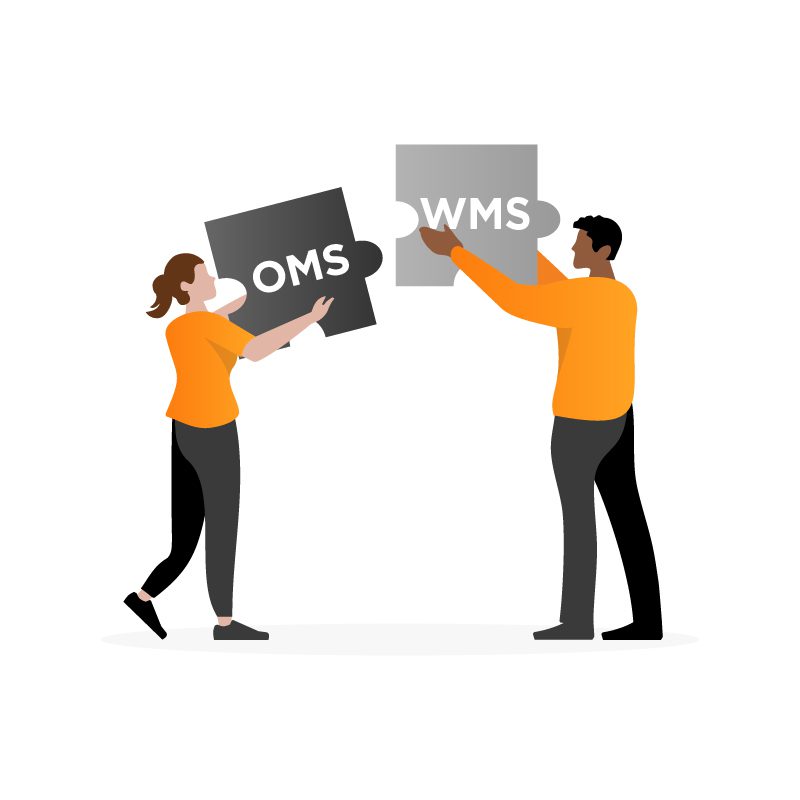
Not all WMS solutions are created equal
Different WMS warehouse software systems are designed to suit different business needs. Some focus more heavily on inventory fulfillment. Some on material handling. Some try to do everything and end up doing nothing excellently. It’s important to understand what these systems do well and not well – along with what you need and do not need (or at least not right away).
Some areas to dig into include:
- The levels of complexity – how easily can it be implemented and learned?
- Installation and licensing – what are the hidden costs?
- System stability – will it break when you add other crucial systems?
- Support – was the solution built or acquired? Do they continuously guide your growth or leave you to fend for yourself with expensive third parties?
- Architecture – what are the limitations and unanticipated costs when you need to improve your warehouse space or expand? Will you have to adapt your processes to fit the system vs. the other way around?
What can a WMS system do for your business?
Consider this: the warehouse order-picking process accounts for 50-55% of total warehouse operating costs! With labor so hard to recruit and retain, a warehouse management system is great at automating parts of your fulfillment operations to offset costs and safeguard against disruptions.
Automation is only one piece of it. What other capabilities will help you step up to the demands of modern commerce and grow in a way that legacy systems never will? Learn the top 6 features of a WMS that your warehouse teams can’t live without.
WMS systems benefit your bottom line and make your day easier
Your company’s ROI (or lack thereof) will depend on how well your warehouse management system can flex with your needs and deliver benefits in eight areas:
- Improved visibility and decision-making: Know exactly what inventory you have, where it is, and the optimal way to deliver it quickly.
- Data analytics and reporting: Understand your customers’ rapidly shifting preferences and present a real-time big business picture of your operations.
- Optimal use of labor and automation: Empower workers to quickly learn modern tools that improve efficiency, safety, recruitment, job satisfaction, and retention.
- Improved warehouse utilization and intelligent routing: Improve layout, space, and capacity inside your facilities while determining the optimal fulfillment location outside the 4 walls to speed delivery times.
- Faster, easier returns processing: Reduce mistakes, time, and overhead spent to get returned products back into your available-to-sell network.
- Faster time to value: <90 days to go live simplifies high-risk IT complexities; white-glove expertise and consistent, vested, ongoing support.
- Keep systems current and integrations seamless: As your business requires evolving capabilities like adding a marketplace, new locations, or other cloud solutions, tap into +150 pre-built WMS integrations.
- Create the best customer experiences: Grow revenues and differentiate your business with fast delivery speeds, streamlined services, personalized products and options, and a 360° view into demand.
Learn how these top 8 benefits of WMS improve the ROI of your project.
Factor | Cloud-Based WMS | ERP or Legacy System |
---|---|---|
Inventory Visibility | Real-time view of exactly what inventory you have, where it is, and how best to deliver it | Hard to access, manual & often unreliable |
Deployment | Go live in <90 days | 9-12+ months or more if customization is needed |
Updates | Sub-second, automatic, real-time data provides one source of truth. Especially helpful in keeping available inventory straight in multiple channels or locations. | Data lag with costly consequences and information your teams can never seem to rely on. |
System Reliability | 100% uptime even during peak means you don’t have to worry. | High risk of outages and syncing problems with critical systems like ecommerce ordering |
Scalability | Fast and easy path to advanced capabilities like OMS and in-store fulfillment—built on a single database and codebase. | Rigid, out-of-the-box functionality. Changes are slow and often involve custom work and expensive consulting you didn’t anticipate. |
Integration | Pre-built integrations to quickly connect other supply chain systems: shipping, ecommerce, ERP/CRM, automation solutions, and more. | Complex; heavy technical skills & involvement |
Cost Model | Subscription model with clearly outlined and predictable costs, including high-touch expert design and post-implementation support. | High upfront investment in a full suite with features you may never need, or may never get support on. Changes often bring hidden fees rather than baked-in flexibility to activate what you need when you need it. |
Tackle cost constraints
56% of retailers say shipping cost is their most significant fulfillment challenge, according to an omnichannel and fulfillment benchmark report led by Retail TouchPoints and Deposco. Throw in inflation, labor, and transportation and logistics challenges, and something’s got to give.
What does not “give” is the consumer’s expectations for product availability; fast, flawless delivery; and buying options that evolve constantly. How do you pinch pennies when nothing less than a perfect omnichannel experience will do?
Read how to reduce fulfillment costs with a WMS.
Make Peak Seasons more profitable
To invest or not to invest? Is it even a question? There’s no time to appreciate the ROI of WMS better than Peak Season. Those January blues kick in and companies decide they never want to go through the “ship-show” they just experienced.
According to our Peak Season report, 92% of supply chain leaders agree that a WMS will prepare their warehouse operations to be more profitable during peak. Of this group, 70% are implementing a WMS now. Not sure how to present the business case and get something in place before the next seasonal rush?
Supercharge ROI During Your Peak Season
And all year long. Understand the short- and long-term ROI of a warehouse management system that can flex year after year.
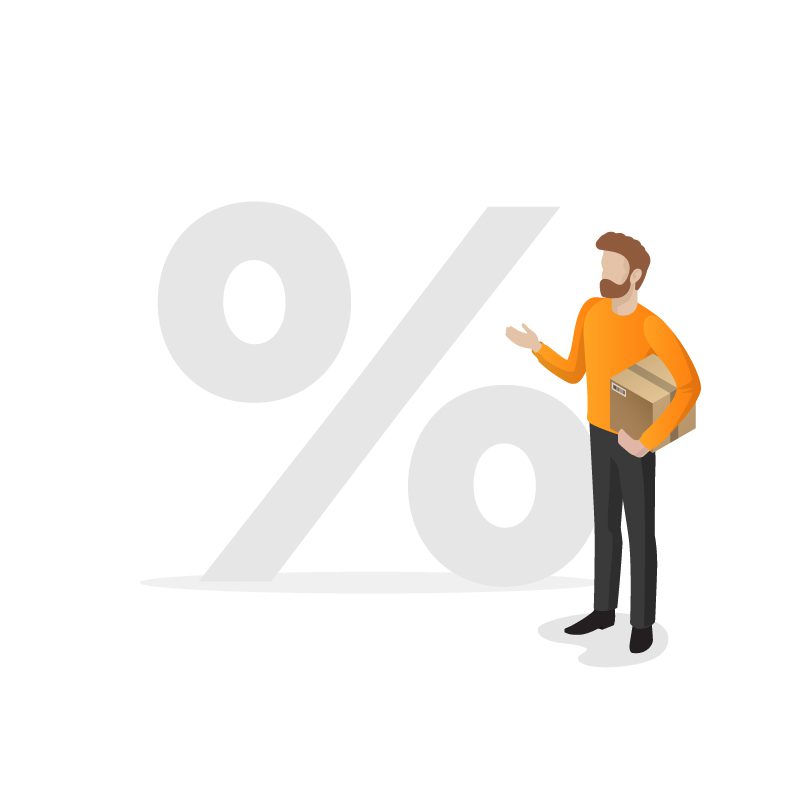
Best practices for adopting warehouse management software
Fix blind spots
Warehouse management systems accelerate your growth by removing costly blind spots in 7 key areas. Fixing these blind spots will open up huge and immediate profitability:
- Enterprise Visibility – Do I know how much inventory I have? Is it accurate?
- Inventory Management and Tracking – Do I know where my inventory is located?
- Real-Time Allocation – Do I know if my inventory has been allocated to an order?
- Labor Costs – How do I manage warehouse staff performance?
- Backorders – How do I eliminate backorders?
- Peak Demand – How do I handle seasonal spikes?
- Online Inventory – How do I show available-to-promise inventory on my website accurately?
Read more: Warehousing methods for boundaryless fulfillment.
Establish the right metrics in WMS
Throughput, error rates, processing cost per unit, and labor efficiency are some of the top WMS metrics that will grow or slow your company. Standardizing and monitoring your KPIs will quickly fix bottlenecks, performance gaps, and inaccurate data to improve warehouse space, resources, labor, and time.
Learn the best warehouse management metrics to track including examples.
Create custom workflows for your process
Creating custom workflows can quickly boost warehouse management performance. By streamlining processes and automating repetitive tasks, you can make operations more efficient and cut down on errors. Custom workflows help keep inventory tracking accurate and improve forecasting, so you’re less likely to overstock or run out of items.
They also make it easier for teams to collaborate by centralizing real-time data and sending automated updates. This enables better decision-making, faster order fulfillment, fewer mistakes, improved compliance, and happier customers — all of which lead to better overall performance and cost savings.
Train team members on software use
Particularly during times when you need temporary warehouse labor, your WMS should be robust, yet easy enough to learn in 15 minutes or less. Fast training and onboarding are essential for addressing labor shortages, reducing turnover, and minimizing customer-facing disruptions. Proper training ensures that employees can efficiently and accurately use the system. Investing in your people improves job satisfaction, job safety, and morale, leading to lower turnover rates.
Use analytics to create predictability
Customers want certainty and predictability when they order products. But what about the certainty of your financial future? With supply chain data analytics and reporting, you can have it.
While it seems that being in warehouse management is nothing but predictable, robust warehouse management systems have turned that around.
Learn how analytics and reporting create predictable supply chains. Or explore our analytics and reporting applications.
Scale with WMS integrations
Leveraging integrations is a best practice in adopting WMS because it gives you flexibility in adapting to future capabilities without requiring extensive in-house IT time or technical expertise. By utilizing cloud-based integrations, your business can seamlessly connect the WMS with other essential systems such as ERP, CRM, shipping, automation, and ecommerce platforms. This interconnected approach allows for real-time data synchronization and streamlined operations, ensuring that the WMS can evolve with changing business needs and technological advancements.
Conquer Uncertainty and Fast-Track Your Supply Chain!
Are you putting new technologies on hold because old ones keep holding you back? Nonsense! Prepare for a complete mind shift that uses flexible WMS integrations to replace reactions with anticipation, strategic risk mitigation, and continuous innovation.
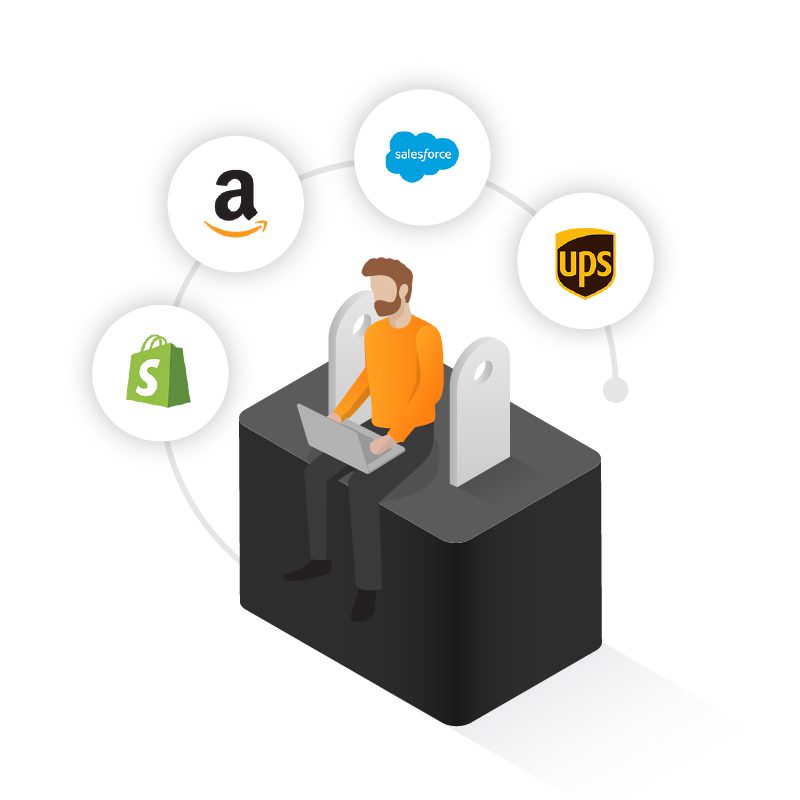
WMS software integrations in a modern platform give you access to ready-made connections to existing systems (ERP, CRM) and future ones you may need: shipping carriers, marketplaces, MHE, and TMS. That means you can significantly lower the cost, time, and technical resources to start seeing value from your investment.
Pro-tip: Some WMS companies consider integrations out of scope. Or they only invest in the bare necessities – for instance, ONLY the 1-2 most common shipping carriers. You need a lot more options! Don’t get surprised by fees added after the project is underway. Ensure your partner is committed to continuously investing in, maintaining, and expanding its integrations library every year.
Cloud integrations managed by the WMS partner will reduce the burden on your internal teams. So your company can focus on core operations while maintaining a scalable and winning tech stack.
Connect your marketplace operations
Shopify and WMS
Are you selling or thinking of selling on Shopify? Shopify is a big part of the sales strategy for many businesses that want to take advantage of high-growth markets like DTC.
A Shopify and WMS integration will make sure that happens without:
- Connectivity problems
- Manual work to connect to your financial systems (ERP)
- Unexpected technology limitations in scaling to other channels
- Problems meeting the requirements of doing business with large retailers/B2B
- Connecting to physical stores later, if you want to and when you want to
- Guesswork on what products to sell
- High churn and return rates
- Poor responsiveness to new consumer preferences, suppliers easier, and new product or service rollouts
Is your fulfillment software world-class? If not, learn how an integrated OMS and WMS solution for Shopify provides super-simple Shopify order fulfillment. Plus, the world-class Shopify experiences your customers expect.
NetSuite and WMS
Inventory management in NetSuite’s ERP has become grueling in the age where volume and complexities have put warehouse teams in peak season mode every day, all year long.
NetSuite is NOT a warehouse management system!
Companies have learned the painful lesson that pureplay supply chain applications in NetSuite can no longer keep up with current demand. Much less identify channels for new growth. A WMS with integrations for NetSuite lets you connect to your ERP and get warehouse management operations into the current decade – while building adaptability to future changes.
Read why your future depends on NetSuite WMS integrations.
Warehouse management for your 3PL
Integrations within WMS systems help a 3PL grow by creating a tech-forward platform that helps them win more business.
Gain efficiencies through an automated 3PL billing process, fully transparent order tracking, and differentiated customer service to increase your cash flow with an incredibly fast time-to-value.
Read how 3PL integrations differentiate your busy third-party logistics company.
Tackle labor and automation challenges with WMS
It’s the worst-kept secret. Everyone’s got a labor problem.
68% of mid-market businesses are struggling to attract talent. To top that off, warehouse worker salaries increased 38% in the last 5 years, according to the latest warehouse worker job outlook from Zippia.
Learn how modern warehouse management systems help you effectively tackle ongoing labor management challenges.
Customers aren’t just excited by creative delivery and next-/same-day shipping. They expect it. In response, companies are investing in these top 5 key WMS automation technologies:
- Mechanization
- Robotics, wearables, and augmented reality (AR)
- Advanced order management and DOM
- Enterprise-grade AI
- Frictionless unified commerce – every sale, anywhere
The flexible architecture of a modern WMS paves the way for these technologies, meeting tough customer demands while achieving healthier margins.
Learn the 5 WMS automation technologies to do more with less.
Support your ESG efforts with a WMS
ESG is requiring companies to rethink order fulfillment for sustainable logistics. In a recent DTC Market report with Industry Dive, 33% of supply chain leaders said their top reason for investing in technology was to make their business operations more environmentally friendly.
Informed decision-making around environmental responsibility ranks high on the priority list for today’s choice consumer. How does your fulfillment solution support that?
Warehouse management systems have a new job description.
Learn how they can differentiate your business: Technology’s role in ESG.
Improve returns management in WMS
The logistical journey of retail returns is getting more expensive! About $500 billion annually, to be exact. But the environmental impact of returns is also well worth examining.
Managing returns with a WMS system can reduce the environmental cost of returns.
Read: Ecommerce returns: the environment also pays.
Buying a warehouse management system
The “why” of implementing WMS is easy. HOW to buy a system for warehouse management is often where companies run into misconceptions, costly surprises, and often stalled growth.
Which WMS software is best depends on what you want to get out of it. Most solutions do a good job of fixing immediate problems. But, few are designed to adapt and get you where you want to be in 10 years with minimal cost or disruption.
Confusing options, misleading noise from salespeople, hidden costs and maintenance, and features you didn’t realize you would need later are common factors leading to regrets.
Learn how to buy the best WMS software for your business.
When can I get value from WMS?
You just saw on LinkedIn that your competitor has a shiny, new WMS. Does that spark a case of FOMO (fear of missing orders)?
What they failed to post is how long the sales cycle and implementation took. That a painful middleware project was required. Or how long it took their staff to learn it. Anyone who has been through a peak season can attest… Timing, need, and fit are everything in your WMS search.
For most growth-minded companies, when you get value can be just as important as deploying the right WMS solution – and the speed of perennial value it will deliver.
Learn why time-to-value is the top factor in your WMS decision.
What’s the cost of WMS?
The cost of WMS can range significantly in the industry. The size of your overall operation and your annual budget will likely have the biggest implications for your WMS costs.
Factors that impact WMS pricing include:
- Number of facilities
- Number of users
- Type of WMS pricing or service model (cloud, on-premise, perpetual license)
- Level of partner support and attention to your unique needs
If you are running a single warehouse operation, you can expect to pay a higher per-warehouse cost for your warehouse management system, both cloud and on-premise.
WMS costs are typically broken down per month for the first year. Cloud WMS systems are typically cheaper than a perpetual license service. On the lowest end of the range will be a small WMS for a single location and single user, without the bells and whistles. On the high end would be a true enterprise-level WMS system that manages multiple sites and requires infrastructure improvements at each.
Estimating and budgeting tips
In estimating the cost of WMS, it’s crucial to understand the end game of your engagement. Does the partner help you set goals outside of fixing problems? You can save significantly on total costs for your WMS by choosing a partner that offers white-glove support and baked-in scalability — such as pre-built integrations architected on a common codebase.
Your partner’s level of support hugely impacts WMS costs in cases where you’ll need to introduce new functionality later. Without it, upgrades will require additional systems, which may or may not work well with your WMS out of the gate.
If they didn’t build room for new capabilities from the ground up, expect long delays and much higher prices, including consultant fees, which will significantly increase as you outgrow your system.
An end-to-end WMS+OMS platform-for-growth partner will clearly outline that journey for you upfront, lowering the overall business cost of WMS.
It’s best to seek out multiple bids based on specific needs. Features that you can designate as ‘must-have’ versus ‘like-to-have’ may make your selection process simpler and easier to keep in line with your overall budget.
Due diligence: rightsize your WMS partner
While there is security in the long-term incumbent, for smaller brands seeking accelerated growth, it can also mean that the partnership isn’t there. How can you make sure your partner is focused on YOUR success?
It’s a lesson borrowed from the Goldilocks story. Of the many options, many are too small. A few are too large, but a handful are just right. The details are important and rarely outlined in the brochure.
Louis Thibault, Senior Director of Operations and Special Projects at Altitude Sports, says his partnership with Deposco has grown so much over the past 7 years. “Looking back, it’s nice to see where we were at the time and where we are today. It still feels like a great decision and a great partnership.”
For Matt Moreman, Obsessed Garage President and Founder, the experience has also been great. “I don’t think I could highly recommend Deposco more. One of my biggest concerns was I didn’t want to get left on an island and they say, ‘Here you go,’ get us all set up, and then walk away. There are always bugs in software, especially when we’re customizing it to what we’re looking to accomplish. [Deposco] has been there every step of the way, and that’s a really important trait.”
So what questions should you be asking yourself? Learn more: 6 Things WMS Companies Left Off Their Brochure.
What to avoid in warehouse management
Knee-jerk WMS decisions at Peak Season
Shopping for a WMS usually starts when a company suffers that January hangover. Over-indulged spending to make up for what was a complete ship-show, despite you doing everything you could do to prevent:
- Seasonal labor, overtime, and onboarding
- Rush shipping fees
- Chargebacks
- Stockouts
- Late, missed, and incorrect shipments
- Angry customers
- Angry supply chain partners
It doesn’t have to be that way ever again. Start early and you can attack peak season all year long.
Discover more tips to remove chaos from your peak season!
The “Nightmare” WMS purchase
No matter what method you use for warehouse management – be it a legacy WMS, ERP system built in 2003, spreadsheets, or something else – there’s one thing we can all agree on: Anything can go wrong in the warehouse at any given moment.
For years, we’ve asked our customers to imagine their worst warehouse management nightmares before Peak Season hits. Then we have a little Halloween fun with it. “Witch” scenarios give them the heebie-jeebies? And how does Deposco WMS protect margins for these customers and keep them growing?
Avoid these Worst warehouse management nightmares.
Implementation tips and WMS software comparisons
When something’s too good to be true, it usually is. The promise of a 45-day or “self-directed” implementation sounds pretty darn excellent – until you learn that not all WMS implementations are the same.
The most misunderstood and value-eroding facts about implementing WMS software are often left out of the sales conversation.
Get the facts: Beware of the 45-day WMS platform implementation.
Compare WMS software tools
All WMS vendors tell you they do pretty much the same thing. They don’t.
Are you getting pressure from all directions to quickly implement a modern WMS system? We’ve seen too many decisions that yielded quick wins but failed to drive growth year after year.
Our free WMS Selection Center offers some great tools to compare WMS options, ensure a productive evaluation, and grow smarter.
What WMS capabilities do you need?
Learn the requirements and intangibles to consider as you prioritize the functionality you need now (and may need later).
Prepare for your WMS RFP
What should you ask to make your WMS system evaluation productive and avoid costly lessons? Download a free proposal worksheet to be more productive with your shortlist:
What can you save with a WMS?
Use our interactive WMS Savings Calculator to instantly estimate your annual savings specific to your company’s operations over the next few years.
Why Deposco
Warehouse management systems are essential for selling more inventory to more customers in more places — better and more cost-effectively.
Created right, right from the start
Despite the confusing array of warehouse managing system options, not all are created equal. The right choice will lead to rapid operational savings, new revenue streams, enhanced customer loyalty, and a comprehensive real-time view of your supply chain.
Unlike traditional ERP systems, modern WMS solutions offer agility, specialized expertise, and a scalable, predictable technology adoption path, making them indispensable to future growth.
Modern warehouse management
Companies come to Deposco after being burned by technologies that are simply signing POs. We uniquely focus on results for the midmarket.
Our long-standing history with customer success proves we are a partner for life. We understand that every customer has unique needs that can’t be served with an out-of-the-box solution that can’t keep up over time. We are accountable and we get the job done no matter what.
Our long list of success stories proves rapid labor and cost savings, volume growth, inventory accuracy, ability to adapt to rapid market changes, and winning customer experiences within 90 days of go-live.
Deposco Bright Warehouse, part of our Bright Suite platform, has snagged some serious industry awards and accolades such as inclusion on the Gartner Magic Quadrant, the Inc. 5000, and product awards from Frost & Sullivan for our integrated WMS and OMS applications. These highlight our leadership in providing top-notch supply chain solutions that help businesses grow and thrive.
Learn more about our platform or grab a demo today!