The 2024 peak season was a wake-up call
58% of supply chains hit critical failure, drowning in manual processes, lost sales, and customer frustration. The traditional path to upgrading supply chain technology—waiting 9-12 months for implementation—no longer works in today’s rapid-fire supply chain environment where customer expectations and customer demands shift by the week.
Download: “The Great Peak Season Reality Check,” a research report by Industry Dive and Deposco.
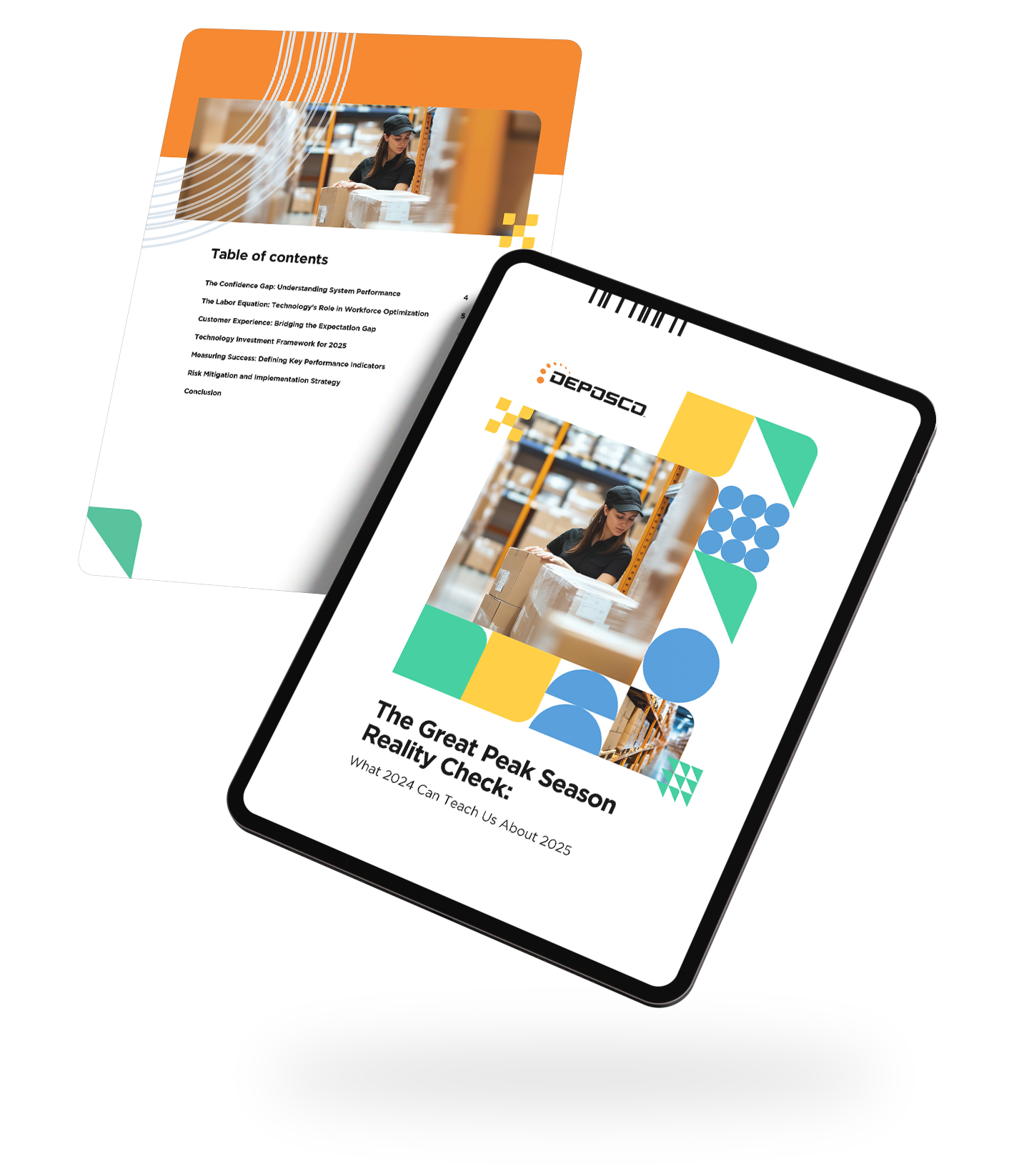
There’s a better way
Modern implementations can go live in 90 days or less, giving you the agility to adapt as your business evolves. This accelerated timeline isn’t just about speed—it’s about staying competitive in a market where waiting a year for new technology means you’re already behind.
By starting now, you can be fully operationally ready by spring, with months to optimize and fine-tune before peak season demands hit.
How to use this plan
This quarter-by-quarter action plan shows you how to transform your seasonal fulfillment operations at the pace of modern retail—turning inventory blind spots into real-time visibility and manual bottlenecks into automated efficiency. Each phase is designed to deliver quick wins while building toward peak season success.
Q1 2025: Foundation building (January – March)
Core fulfillment focus:
- Deploy core warehouse management capabilities to improve efficiency and accuracy through waving, directed activities, and real-time inventory views.
- Conduct an inventory accuracy assessment across all storage locations, leveraging real-time visibility.
- Do a peak season retrospective to document fulfillment bottlenecks and prevent recurrences. Were there breakdowns in picking and packing? Where did throughput slow and impede order flow?
- Establish labor efficiency benchmarks to measure improvement areas. Defining them based on the 75th percentile of current activities can set an achievable target for a majority of roles.
- Optimize storage slotting based on demand patterns and product velocity. By locating fast-moving items closer to the picking aisles, you can reduce travel time and improve order fulfillment speeds.
- Address just-in-case vs. just-in-time inventory imbalances to avoid unnecessary overstocking, overselling, or shortages. What buffer stock do you need to operate with, and do you have enough variation that a supply chain planning solution would be beneficial?
Learn how warehouse management software directs core fulfillment processes for operational excellence.
Order management priorities:
- Refine order routing logic to ensure the most cost-effective and efficient fulfillment based on real-time order flow and inventory positioning.
- Evaluate channel allocation rules for peak season prioritization, ensuring fulfillment network resilience. Segmenting channels and fulfillment methods will allow you to resource-plan and execute more efficiently.
- Strengthen the returns process to handle increased post-peak volume by implementing streamlined return paths and predictive restocking strategies. Empowering customer sales reps with dedicated order workbenches can streamline the returns process and increase customer satisfaction.
New to OMS systems? Get a detailed introduction: the benefits, key capabilities, how OMS fits into omnichannel, and where to start.

Advanced technology assessment:
- Consider AI-driven demand forecasting for better labor and inventory planning with continuous refinement based on live data streams.
- Identify supply chain automation opportunities in picking and packing operations to alleviate labor shortages and reduce manual errors. Use a smaller pilot to determine if the ROI structure for the automation works for your organization.
- Benchmark against supply chain best practices to enhance efficiency in order cycle times and minimize disruptions. Understanding when you have achieved the most you can from a process allows you to prioritize more impactful investment areas.
- Leverage intelligent supply chain solutions to integrate fragmented systems and remove dependency on clean data, creating end-to-end operational transparency. Siloed inventory optimization has limitations and can cause unintended negative impacts.
Can your fulfillment system support the integration and automation necessary to grow with your business?
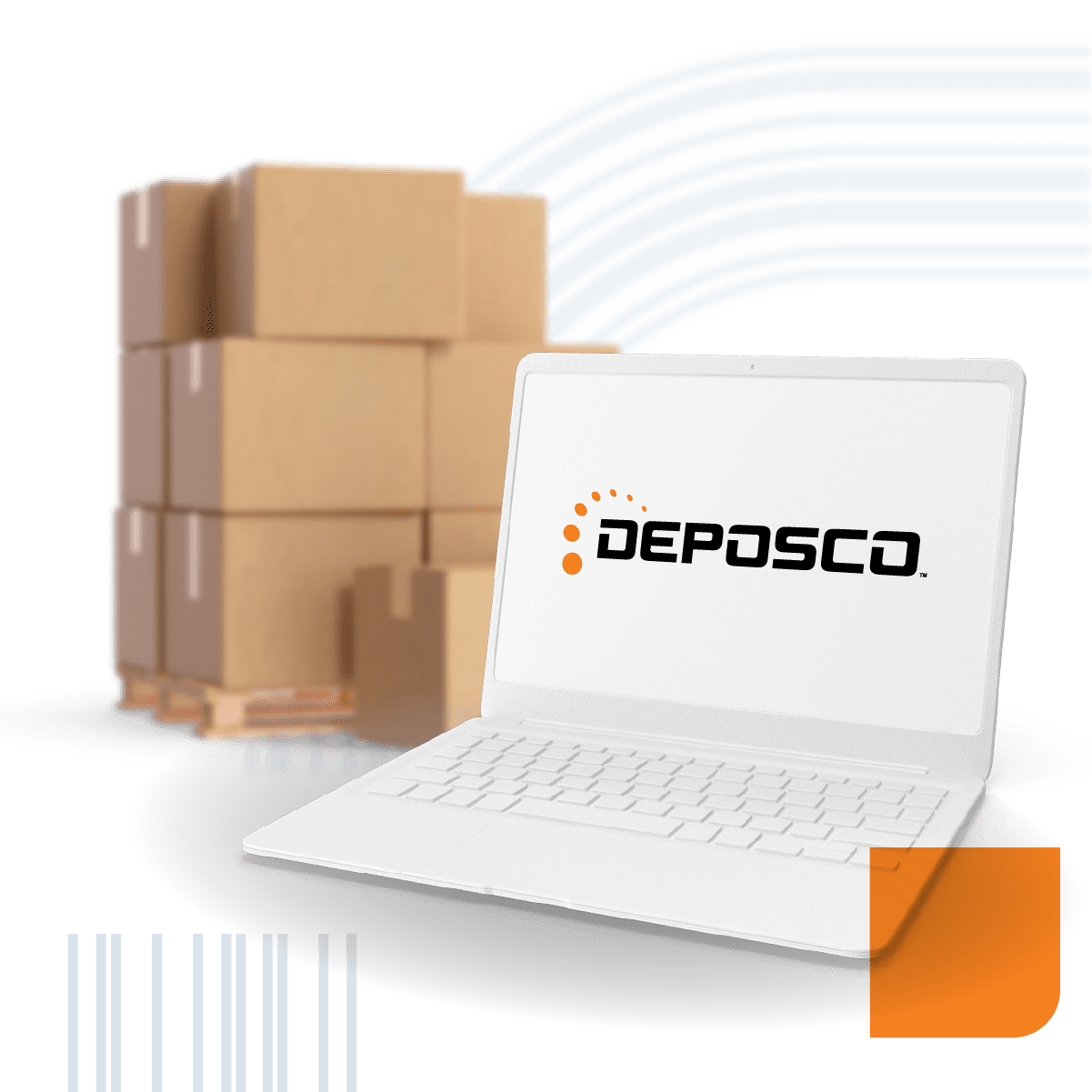
Key success metrics:
- Core systems live within 90 days or less
- Real-time inventory visibility established
- Baseline labor and efficiency metrics in place
Q2 2025: Implementation phase (April – June)
With the foundation set, Q2 focuses on implementation and execution, ensuring technology delivers immediate value. This phase transitions from planning to scalable operational improvements that will support peak demand.
Fulfillment enhancements:
- Expand mobile picking applications based on Q1 data insights to improve order processing speed. With real-time mobile direct, opportunities arise for priority or value-added orders that drive revenue.
- Implement cross-facility inventory visibility for enhanced stock distribution and better fulfillment flexibility. Combined with the right planning and order management solution, you can reduce overall shipping spend by 2-5% by reducing shipping distances.
- Deploy automated packing to reduce labor-intensive workflows and increase throughput per shift.
- Enhance order routing logic using predictive analytics to optimize decision-making based on cost, distance, and carrier performance.
- Integrate labor reporting to match workforce allocation with demand spikes, reducing overstaffing and burnout.
Order management updates:
- Activate distributed order management (DOM) for dynamic order allocation and faster fulfillment routing. DOM automates order allocation, reduces ship times, and increases customer satisfaction.
- Optimize carrier selection automation to minimize shipping costs while maintaining delivery speed. Rate shopping allows for savings scenarios that can be captured as revenue for outperforming contracts.
- Ensure seamless ERP and supply chain software integrations for improved procurement and inventory management visibility across nodes. Free up ERP to do what they do best and eliminate the time delays associated with financial systems.
Enhance decision-making with automated order management and DOM execution.
Intelligent systems:
- Deploy predictive labor planning models to address workforce shortages through AI-driven allocation strategies.
- Implement automated inventory replenishment to prevent stockouts and keep critical SKUs consistently available.
Key success metrics:
- Cross-facility operations fully integrated
- Automated systems performing at target efficiency levels
- Staff proficiency with advanced warehouse tools
Q3 2025: Advanced capabilities & testing (July – September)
Q3 is the stress-test phase. Organizations must refine advanced capabilities and simulate peak conditions to ensure operational resilience. Last-minute implementations and untested systems result in costly failures, making proactive testing essential.
Warehouse operations:
- Deploy multiple picking strategies for improved labor efficiency and reduced pick errors. Single lines and multi-lines, priority, bulk, non-conveyable, and other variations allow your workforce to be more predictable, productive, and error-free.
- Implement cartonization software logic to optimize packing density and reduce shipping costs. Carton density works with features like order consolidation to ensure you have the lowest-cost profile per shipment.
- Fine-tune dynamic put-away rules to adapt to peak season fluctuations, ensuring a continuous flow of high-demand SKUs to reduce labor travel.
- Conduct stress testing under simulated peak conditions to assess system load capacity and ensure agile, real-time fulfillment.
- Develop and validate contingency protocols for rapid incident response to potential order spikes or system failures.
Order orchestration:
- Configure peak-season routing rules to align with shifting demand trends and fulfillment SLAs.
- Optimize backorder management processes to reduce order delays and improve customer retention.
- Deploy intelligent order-splitting algorithms for efficient, multi-node fulfillment with minimized last-mile costs.
- Utilize AI-enhanced demand forecasting to manage volatile consumer confidence shifts and ensure adequate inventory planning.
Predictive capabilities:
- Refine demand-driven replenishment strategies using AI-powered insights and real-time marketplace conditions.
- Implement real-time KPI dashboards to monitor warehouse performance and proactively adjust labor distribution.
Which KPIs will best move the needle, keeping your performance in continuous improvement mode?

Key success metrics:
- Successful peak stress tests completed
- Peak routing and contingency plans validated
- Platform optimizations improving order processing speed
Q4 2025: Peak season execution (October – December)
The final phase is all about execution, agility, and rapid response. With automation and forecasting tools fully operational, organizations must monitor performance, adjust dynamically, and ensure seamless peak season fulfillment.
Fulfillment optimization:
- Activate pre-tested surge capacity protocols to manage unexpected volume spikes with preemptive labor and fulfillment adjustments.
- Deploy real-time labor management dashboards to dynamically allocate workforce and minimize downtime.
- Implement automated exception handling to resolve fulfillment bottlenecks instantly without human intervention.
- Optimize multi-carrier shipping to ensure cost-effective, high-speed deliveries aligned with peak demand shifts.
- Enable overflow facility routing to prevent fulfillment slowdowns and manage inventory imbalances dynamically.
Rate Shopping, part of our Shipping Management solutions, can reduce your shipping costs by 2-20% in just a few clicks.

Key success metrics:
- Real-time KPIs meeting operational targets
- Automated response systems handling exceptions efficiently
- Labor efficiency goals achieved
The competitive edge: why now?
Peak season success isn’t built in Q3 or Q4—it’s built all year long. Companies that procrastinate find themselves in crisis mode, incurring unnecessary costs and operational failures.
By following this structured, technology-driven roadmap, your business will not just survive peak season—but thrive in it. Modern supply chains demand agility, automation, and proactive execution, all of which are possible with the right strategy and WMS solutions.