Your warehouse is sitting on untapped goldmines of efficiency. What can you do with MHE warehouse solutions? More importantly, what do you need to get there?
The numbers tell the story
79% of high-performing supply chains outpace competitors in revenue growth, while 55% of forward-thinking companies are doubling down on supply chain tech investments. With labor costs surging 13% since 2019 and 60% of organizations preparing to invest over $1M on warehouse technology, the margin for error has vanished.
Just ask Altitude Sports, which slashed pick-pack-ship costs by 20% through strategic automation. The real victory isn’t installing fancy conveyor belts or robots—it’s building the technological foundation that transforms your warehouse from a cost center into your company’s secret weapon.
While MHE automation options range from simple physical structures to full automation features, your focus should be on the foundation that supports and evolves your strategy. At a time when capital is lean, making the right decisions around timing, selection, and investment is table stakes.
Inside this guide
- Critical Considerations for MHE Investment: Timing Your Warehouse Technology Decisions
- Assessing Complexity & Maturity: A 10-Dimension Framework
- Navigating Software Integrations: Navigating the WMS, WES, and WCS Ecosystem
- The Power Triangle: Intersection of Automation + Robotics + WMS, in perfect sync
- Implementation Roadmap: Phases, Readiness, Key Success Factors for MHE Success
When is the right time to expand into supply chain automation? Is there a volume threshold you should monitor? Which MHE warehouse solutions—robots, cobots, autobaggers—will best serve your product assortment today and tomorrow? These are urgent questions for supply chain leaders as rising consumer expectations, labor constraints, and technological advancements drive warehouses to evolve from cost centers into strategic advantages.
Deposco helps businesses future-proof their technology decisions with go-live in 90 days. No guesswork. No giant dev team required. Discover the fastest route to operational excellence and adaptability. Schedule a personalized strategy session.
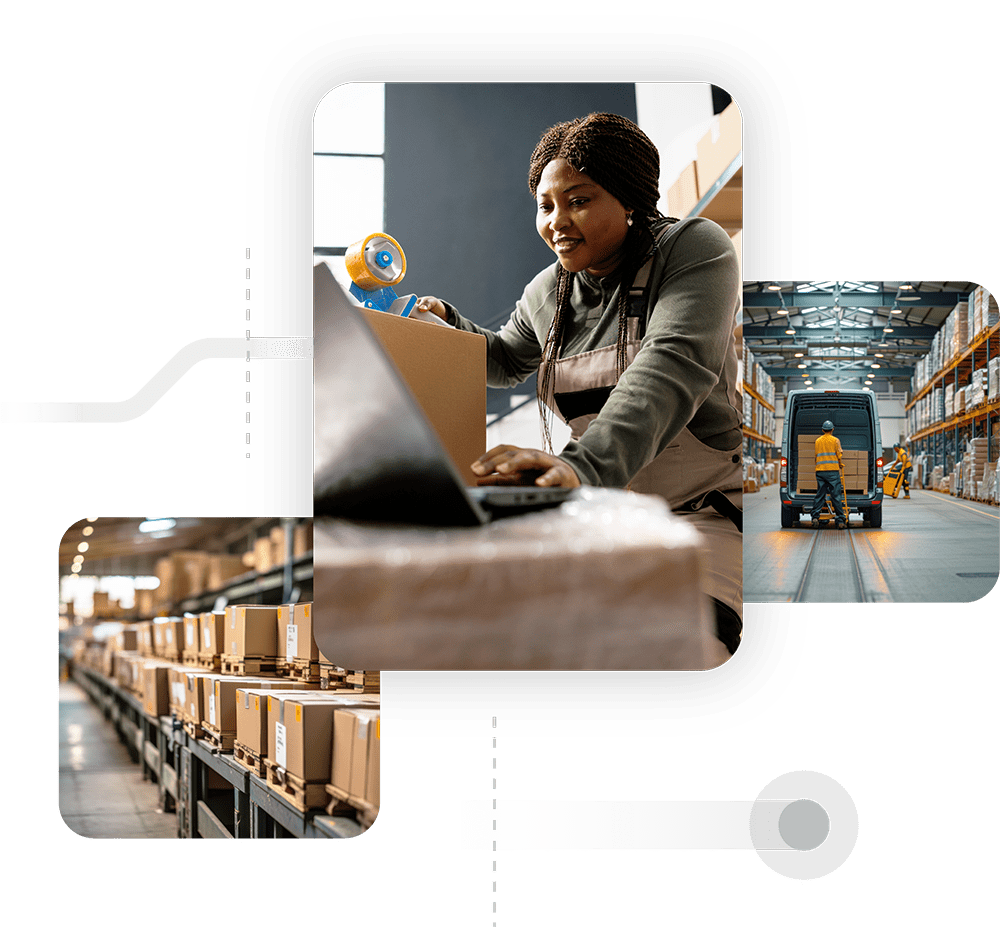
Based on industry research and expert analysis, this guide presents a framework for assessing your warehouse management maturity and selecting solutions that accommodate both current needs and future growth. By understanding the complete warehouse technology stack, you can make informed decisions that deliver immediate value while positioning for long-term success.
Critical considerations of MHE warehouse solutions
The evolution of warehouse operations
Over the past decade, warehouse operations have undergone a remarkable shift from a perceived cost center to a strategic differentiator. This transformation is largely the result of ecommerce’s explosive growth, which has permanently altered buying habits and fulfillment expectations.
Ecommerce growth
Ecommerce now accounts for over 20% of retail sales globally—requiring warehouses to implement new picking, packing, and shipping processes that go far beyond the traditional retail distribution model. In parallel, rising consumer expectations for lightning-fast delivery, real-time visibility, and flexible fulfillment options—including buy online, pick up in store (BOPIS) and same-day delivery—have pushed organizations to develop increasingly sophisticated operational capabilities.
Labor hurdles
Complicating matters further, persistent labor shortages and rising wages in warehousing have created a competitive scramble for workers, spurring both efficiency improvements and the adoption of technologies like robotics, AI, and advanced labor management software. These innovations have advanced rapidly, offering new avenues for operational excellence and resilience.
Tariffs and other global disruptions
Meanwhile, recent global events—from pandemics to tariff impacts and geopolitical disruptions—have exposed how vulnerable supply chains can be, driving organizations to fortify their distribution networks and explore new fulfillment strategies. As one industry expert aptly observes, “What got you here won’t get you there.”
Companies that once relied on purely manual processes or basic warehouse processes now confront a more complex reality that demands forward-looking solutions like MHE in the warehouse and a keen strategic vision.
The Technology Challenge
The first step is understanding what is available and how that matches your prioritized needs. And it is not easy to do, the warehouse technology landscape has become increasingly complex and is directly tied to your assortment, location, workforce and much, much more. Organizations must navigate a tremendous array of options:
How do you determine which is right for your organization? This proliferation of technology options creates what some call “analysis paralysis”—with companies struggling to determine which solutions best match their needs and how different systems should interconnect.
The risk of “shelfware” (purchased but unused technology) or failed implementations is substantial.
The need for a maturity perspective
Deciding on the right technology starts with a firm grasp of current operational challenges and a clear view of where your business is headed.
Ask yourself: Is throughput struggling because of labor limitations, or are multi-step manual processes slowing things down?
A maturity model approach offers a holistic way to understand these pain points. By accurately assessing your present level of warehouse complexity and mapping out suitable technology matches, you can prioritize flexible solutions that not only address pressing concerns but also support future expansion.
This phased, strategic method delivers immediate MHE ROI while minimizing the risk of over-investing in unneeded capabilities. In the next chapter, you’ll find a comprehensive warehouse maturity framework designed to help you select MHE warehouse solutions that will adapt to your evolving operational needs.
10 dimensions of warehouse complexity and maturity
Warehouse complexity is multifaceted, extending far beyond simple measures like square footage or order volume. Industry research identifies 10 critical dimensions that collectively determine operational complexity:
Each dimension exists on a spectrum from simple to highly complex. For example, MHE Automation might range from completely manual operations to fully automated facilities with multiple integrated systems.
Understanding these dimensions provides a holistic view of warehouse complexity that guides technology selection.
A high-volume operation with simple product characteristics has different requirements than a lower-volume operation handling complex items with significant variability.
The Warehouse Management Maturity model
The median operates between 2-4
Building on these complexity dimensions, we can define five distinct levels of warehouse management maturity:
Many organizations operate within Levels 2 through 4, progressing gradually as their operational requirements become more complex.
The takeaway
You should invest in technology suited to your current level of maturity, while ensuring those solutions can scale to meet future needs.
MHE automation: a critical complexity factor
Among the 10 dimensions of warehouse complexity, MHE automation plays a uniquely pivotal role.
What Level 5 looks like
Industry research indicates that any organization scoring a Level 5 in MHE automation— characterized by extensive use of advanced equipment and a highly automated environment— automatically achieves an elite rating in the area of overall complexity, a distinction not observed in any other dimension.
This complexity arises from the sophisticated management systems required to support automated operations and the intricate integration between warehouse management systems (WMS) and automation control systems.
Coordinating human labor alongside automated processes adds another layer of complexity, while substantial investments in automation necessitate maximizing throughput and efficiency. As warehouses increasingly adopt automation and robotics, managing this dimension becomes crucial for selecting effective technology solutions.
Navigating software integrations
The warehouse management software ecosystem
The warehouse software landscape encompasses multiple specialized systems that serve different functions within the operation. Understanding these distinctions is crucial for making appropriate selections:
The MHE integration challenge
End-to-end visibility is vital for optimizing your supply chain, yet it can inadvertently create friction points. One of the biggest hurdles in warehouse technology is weaving together the many systems that manage different parts of the operation, a challenge that intensifies as complexity grows.
Consider how a WMS needs to link with an ERP such as NetSuite for inventory synchronization and order flow. Or how a WCS must connect with physical equipment to execute commands and handle exceptions.
Layer in additional components—like a WES that balances workloads, or robotics software that updates task statuses in real time—and each new integration point becomes a potential source of friction, data misalignment, and performance bottlenecks.
Bright Socket’s supply chain integrations bring all data into a single, real-time view. Connect systems you already use such as ERP, CRM, marketplace, and other systems. Bright Socket facilitates connecting systems with 150+ pre-built software integrations, which significantly reduce costs and implementation time.
When multiple vendors enter the picture, each with its own protocols and data structures, that complexity multiplies. As a result, organizations have a few main choices to consider.
Companies often make the mistake of sourcing the top solution for each specific need, but that will require a significant effort to integrate everything. A single-vendor suite tends to be simpler to connect, but sometimes misses the specialized features of niche systems.
Another route is an end-to-end platform approach, such as Deposco, which uses an integration layer to unify and manage diverse systems.
Finally, there’s the option of phased evolution—rolling out essential functionality first and expanding capabilities as needs develop.
Ultimately, the ideal strategy hinges on factors like organizational maturity, in-house technical expertise, operational demands, and growth objectives.
Selecting the right software to support warehouse operations
Based on industry research, organizations have nine distinct options for supporting warehouse operations, particularly when automation is involved. These options correlate with different maturity levels and operational profiles:
The nine options of support
The selection between these options depends on current operational maturity, future growth plans, existing technology investments, and risk tolerance.
Right-size your investment
Organizations should resist the temptation to over-invest in capabilities beyond their current maturity level unless there is a clear, near-term transition plan to utilize those capabilities and an expert partner to guide that journey.
Here’s what to look for:
Architectural flexibility
- Look for modular designs that rely on configuration rather than custom code.
- APIs or webhooks should streamline integrations with other platforms.
- Consider on-premise, cloud, or hybrid deployment based on your operational needs.
Scalability
- Ensure the WMS can manage peak seasons, expanded order volumes, and multi-site operations.
- Confirm it supports growing numbers of users without compromising performance.
Technology foundation
- Modern, cloud-native architectures (microservices, containerization) simplify updates. Mobile-friendly solutions enhance efficiency for workers on handheld devices.
MHE warehouse solution readiness
- Even if you’re not deploying robotics soon, plan for it.
- Look for out-of-the-box connectors so you can test automation at a small scale first.
Intelligence and optimization
- Real-time data and analytics open the door to forecasting labor needs and refining picking routes.
- Integrated dashboards and robust reporting drive continuous improvement.
Vendor traits and total cost
- Assess the provider’s innovation roadmap, industry expertise, and partner ecosystem.
- Clarify licensing structures, implementation fees, and upgrade costs to avoid surprises.
By examining each of these dimensions—architecture, scalability, technology foundation, automation readiness, intelligence and optimization, vendor expertise, and total cost—you can narrow down the solutions that will not only address your current needs but also keep pace with the dynamic landscape of modern warehousing.
Common pitfalls to avoid during your technology selection
Many organizations make mistakes unknowingly when choosing warehouse management technology. Acknowledging these risks—and proactively planning for them—helps you sidestep common traps and achieve smoother deployments:
1. Overbuying capabilities
Implementing advanced features before you’re operationally ready often results in unused functionality, inflated complexity, and diminished ROI. While it’s important to plan for future growth, it’s equally critical to avoid over-customizing or adopting processes your team cannot fully support or leverage yet.
Use base flows
One way to stay on track is to begin with the solution provider’s out-of-the-box or “base” flows. These prebuilt workflows are designed to handle fundamental warehouse operations with minimal setup. Adopting these standard flows has several benefits:
- Reduced Complexity: Less customization means fewer integration points that can break or require constant updates.
- Faster Implementation: Out-of-the-box workflows allow teams to go live sooner, lowering time-to-value.
- Lower Costs: Custom solutions can quickly drive up expenses, including higher consulting fees and ongoing maintenance.
- Easier Scaling: You can layer on additional features once your organization has the operational maturity and resources to support them.
By choosing technology that aligns with your current needs—and leaving room to grow into advanced functions later—you’ll strike a balance between innovation and practicality. This approach maximizes both your immediate return on investment and your long-term success.
2. Underestimating integration complexity
Integration among MHE, WMS, ERP, ecommerce platforms, and other systems often becomes the biggest obstacle both during and after deployment. If overlooked, it can lead to budget overruns, delayed timelines, and an ongoing maintenance burden.
- Predefined Integrations: Legacy or ‘out-of-the-box’ vendors come with out-of-the-box connectors that shorten deployment time and reduce errors by eliminating custom coding. However, they may lack the flexibility to handle unique workflows or data formats—sometimes requiring extra configuration or custom development.
- Integration-as-a-Service: Some providers partner with specialized “integration-asa-service” firms, offloading the technical complexities and freeing in-house teams to focus on strategic goals. This setup also promotes best practices and future scalability.
- Defining Key Endpoints: Identify critical endpoints early, such as order data, inventory levels, and shipping status. Ensure your WMS solution supports a repeatable, scalable integration approach for these essential connections.
By tackling integration requirements up front—leveraging predefined connectors and, when necessary, integration partners—you can mitigate risk, streamline deployment, and realize faster ROI.
3. Neglecting user experience
Even the most advanced system won’t deliver full value if employees resist it. Poorly designed interfaces, overly complex workflows, or inadequate training often prompt users to devise workarounds—undermining the ease of use and efficiencies that are possible with the right solution.
For instance, a 10-second delay in printing packing slips might seem inconsequential, but multiplied by 100,000 orders per week, those incremental seconds can quickly translate into missed shipping windows and mounting labor expenses.
To prevent these issues, it’s essential to streamline every step of the workflow so tasks can be completed quickly and accurately. Along with designing user-friendly interfaces that make crucial information easy to find, organizations must also equip teams with sufficient training and communicate the benefits of the new system.
By involving users throughout the transition—encouraging feedback and sharing progress—companies foster adoption while continuously refining processes. In short, prioritizing user experience alongside technical capabilities is key to minimizing friction, avoiding ad-hoc solutions, and reaping the full advantages of warehouse technology.
4. Focusing on technology over process
No matter how cutting-edge a warehouse system may be, it can’t fix poorly designed workflows. Trying to force a “round peg in a square hole” by layering sophisticated technology on top of a flawed operation often results in wasted investment.
Instead, ensuring that the technology is designed to fit the process will yield the best results.
Examples of this
If your operation handles a high volume of single-line, single-quantity orders, consider grouping them into targeted waves. This allows a focused pick-andpack flow that can be completed more efficiently.
On the flip side, bulk orders may benefit from a forward-picking approach, where frequently accessed items are staged in a separate area to reduce travel time. By choosing strategies that align with your actual order profile and fulfillment requirements, you can tune each workflow for maximum throughput.
A structure designed for success
When you introduce advanced solutions—such as automation, robotic picking, or AI-driven order orchestration—you’ll be applying them to a structure designed for success. That’s how you ensure technology acts as an accelerator rather than a bandage for broken processes.
By aligning your operational methods with the demands of your business, and then layering in the right tools, you’ll build a foundation that supports efficiency, scalability, and exceptional customer service.
Automation, robotics, and WMS in perfect sync
MHE warehouse automation is accelerating at an unprecedented growth rate. Industry research indicates that by 2028, 80% of warehouses and distribution centers will deploy some form of warehouse automation. By 2030, one-third of all medium to large warehouses will have at least one operational robotics platform.
Five main factors are driving the acceleration of MHE warehouse solutions:
- Labor Challenges: Persistent shortages and rising costs
- Technology Maturation: Increased reliability, desire to lower operational costs
- Operational Pressure: Higher throughput requirements, faster fulfillment expectations
- Competitive Necessity: Automation as table stakes for high-performance distribution
- ROI Improvements: Faster payback periods, flexible deployment models
The automation landscape has expanded dramatically beyond traditional fixed infrastructure (conveyors, sorters, ASRS) to include various forms of mobile robotics, collaborative systems, and hybrid human-machine workflows.
Emerging automation technologies
Several automation technologies are transforming warehouse operations:
Five things you’ll need to support MHE warehouse solutions
Ever wondered if you’re truly ready to integrate robotics, conveyors, or any form of high-speed automation into your warehouse?
The secret often lies in your foundational WMS software. Before rolling out new hardware, it’s worth asking: Does my current technology stack support the real-time demands and complexities of MHE solutions and workflows?
If you’re not sure, here’s a closer look at the five capabilities you’ll need for a smooth and profitable transition.
- Real-time processing: MHE warehouse automation systems don’t wait around; they function at machine speed, often requiring millisecond-level responsiveness. Your warehouse management software must instantly process transactions, make decisions, and transmit instructions— otherwise, it turns into a choke point. Think about a robotic picking arm that pauses every few seconds, waiting for updated inventory data. That delay snowballs when multiplied across hundreds of picks per hour. Real-time software ensures every pick, pack, and movement keeps flowing without interruption.
- Exception handling: No automation process is perfect. Robots can get stuck, sensors can fail, and items can be misplaced. Your software should detect these hiccups, initiate fallback procedures, and notify human teams only when necessary—say, if a robot drops a fragile item or can’t locate a bin. By smoothly blending automated processes with human intervention, you avoid large-scale operational snarls and keep throughput high.
- Resource optimization: Picture multiple autonomous systems picking orders simultaneously while robotic vehicles shuttle goods to packing stations. Without software that balances workloads, sequences tasks, and prioritizes critical orders, you might find some lines backed up while others sit idle. Resource optimization ensures each piece of equipment, and every worker, operates at peak efficiency—maximizing throughput and preventing bottlenecks.
- Visibility and control: When robots and humans collaborate, having a real-time view of performance is crucial. Can you quickly see which orders are in progress, which machine might be nearing capacity, and how close you are to meeting cutoffs? A robust WMS should give you comprehensive visibility and the tools to intervene when necessary. That could be as simple as rerouting tasks to avoid missed shipping windows or alerting a technician before a machine breaks down.
- Flexible orchestration: Today’s automated setups often look like a patchwork of solutions from different vendors. Maybe you have a robotic picking system in one area, an autonomous mobile robot for shuttling goods, and an ASRS (automated storage and retrieval system) handling bulk inventory. Without a software “maestro” directing these varied components, you wind up with siloed islands of automation. A modern WMS orchestrates workflows across all your equipment, unifying them into seamless processes that eliminate wasted steps and strengthen your operation
By ensuring your software can handle these five capabilities, you’ll be prepared to make the most of your MHE warehouse solution investment—gaining efficiency, consistency, and real insight into what’s happening on the floor. The result? Faster fulfillment, happier customers, and a clear path for measuring the ROI of your automation journey.
Looking ahead: multiagent orchestration and unified control
The next frontier in MHE warehouse solutions
As automation continues to expand, the real challenge isn’t simply deploying more robots— it’s coordinating them all with human workers and existing equipment. Two emerging concepts hold particular promise for bridging this gap and ushering in a new era of seamless orchestration: Multiagent Orchestration (MAO) Platforms and Unified Control Systems (UCS).
Multiagent Orchestration (MAO) Platforms
Ever picture a bustling warehouse with different robots from multiple manufacturers—some shuttling goods to picking stations, others transporting pallets, and still more traveling side by side with human associates? MAO platforms act like traffic controllers in this scenario, dynamically assigning tasks and managing robot paths to prevent collisions or downtime.
By placing a unified orchestration layer above these various systems, the WMS doesn’t have to juggle countless communication protocols or device-specific rules. Instead, it talks to the MAO platform, which translates instructions to each piece of equipment behind the scenes. This simplifies integration while boosting overall efficiency and safety.
Unified Control Systems (UCS)
Imagine if you could manage all warehouse automation—from older conveyor belts and ASRS like AutoStore to advanced collaborative robots—using just one overarching control layer. That’s the idea behind UCS.
Although still largely aspirational, a unified control system could eliminate the patchwork of vendor-specific interfaces and reduce the complexity of maintaining diverse technologies. The ultimate goal? A single “command center” that keeps everything running in harmony, cutting down on integration headaches and allowing for rapid scaling or changes in warehouse processes.
Quick Checkpoint: Does your WMS align?
Organizations looking to automate should keep a close eye on how their WMS strategy accommodates or integrates with these two forward-thinking approaches. For some, it may mean selecting a WMS that seamlessly plugs into MAO platforms; for others, it could mean positioning themselves for a future evolution into a UCS model.
Either way, planning for these emerging solutions helps safeguard against technological dead ends and ensures your automation investments can adapt as new innovations arise.
Implementation roadmap: phases, readiness, key success factors
Why phased implementation approaches work
Successful warehouse technology implementations typically follow a phased approach, delivering incremental value while managing risk and complexity. A maturity-based implementation strategy might include:
This phased approach delivers several advantages:
- Earlier ROI realization through incremental value delivery
- Risk management through contained scope for each phase
- Organizational learning and adaptation between phases
- Opportunity for course correction based on operational feedback
- Alignment of technology implementation with organizational maturity
Technology readiness assessment
Implementing a new MHE warehouse solution isn’t just about flipping a switch—it’s about ensuring every aspect of your operation is prepared for the journey ahead. A thorough readiness assessment can help you spot potential roadblocks and address them early, setting the stage for a smooth transition. This assessment typically covers four major areas:
Key implementation success factors
Research shows that certain factors consistently lead to successful warehouse technology rollouts.
- Set a realistic timeline and scope. It’s tempting to rush an implementation to coincide with a new facility opening or a peak season, but compressed timelines often result in skipped steps and heightened risk. Build a schedule that includes appropriate contingencies and resist the urge to tack on extra features at the last minute.
- Cross-functional engagement. Implementations involve many stakeholders—from operations and IT to finance and customer service. Involve these groups early, gather their requirements, and keep them in the loop as milestones are met or changes arise. Fostering transparent collaboration avoids unforeseen hurdles and helps secure buy-in across the organization.
- Process-first mindset ensures you’re tackling operational inefficiencies before introducing new technology. Automation can amplify good processes—or make flawed ones worse. By refining workflows and standardizing best practices in advance, you give your technology a solid foundation to build upon.
- Phased value delivery is usually the most pragmatic approach. Rather than aiming for an all-at-once launch, consider rolling out high-impact features first, then expanding as you learn what works (and what doesn’t). This approach not only reduces the risk of massive disruptions but also helps your team become comfortable with new tools in iteratively.
- Comprehensive testing drives successful projects. Warehouses are dynamic environments where real-life conditions—like peak traffic, hardware failures, and human error—can’t be fully captured on paper. From unit tests to integration tests to fullscale volume and stress testing, a robust plan will let you catch and fix issues before they hit production.
- Post-implementation support can’t be underestimated. Once the system is live, it moves from being a project to being the backbone of daily operations. Put a formal plan in place for knowledge transfer, ongoing optimization, and any handover tasks needed to keep the new solution running smoothly.
Get printable PDF versions of the chapters in this guide. Share them with your leadership team and anyone around you struggling to work faster. Your next opportunity with MHE warehouse solutions is only 90 days away!
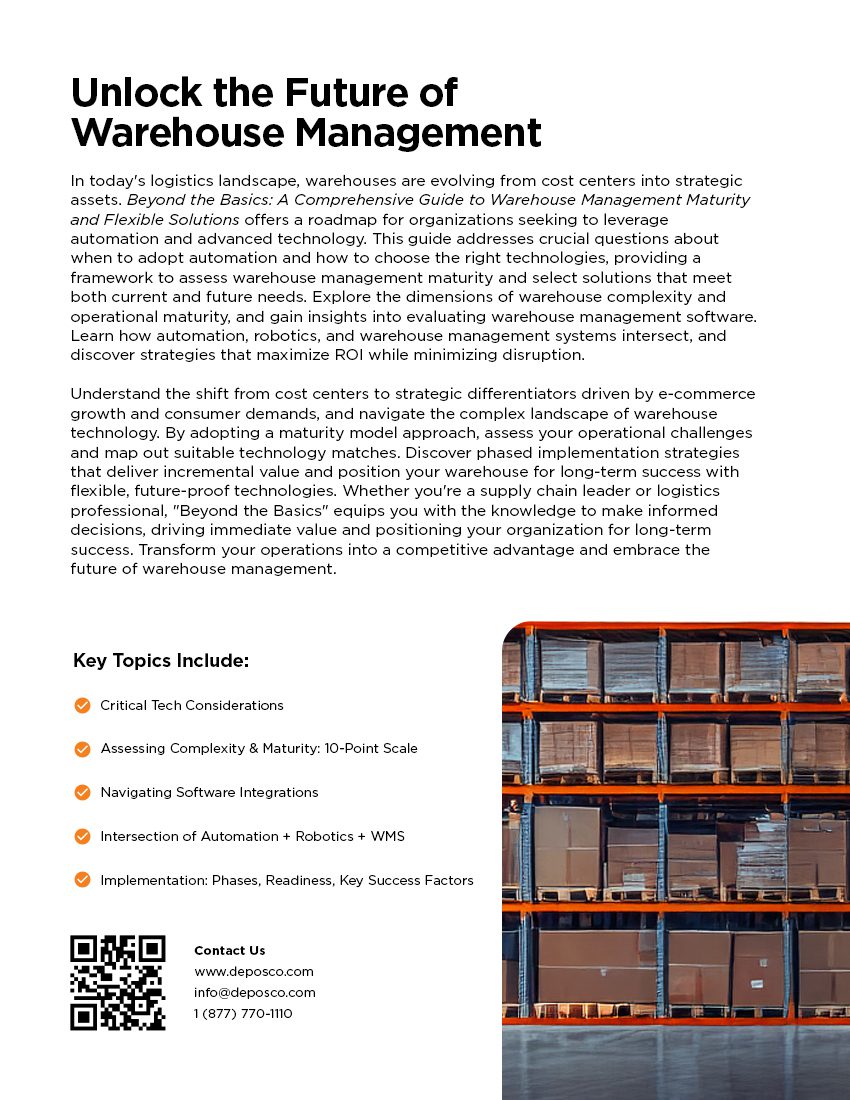
Evolving with purpose
Warehouse operations are no longer just about storing goods and shipping them out the door. Today, they’re a central driver of customer satisfaction and competitive differentiation. Success demands a deliberate and disciplined approach to technology selection—one that starts with assessing your current maturity, pinpoints areas for improvement, and proceeds in managed phases.
Key Reminders:
- Know Your Starting Point: Accurately assess your current warehouse complexity and maturity level using a structured framework.
- Match Technology to Maturity: Select warehouse management solutions that align with your current operational complexity while providing room for growth.
- Prioritize Flexibility: Choose systems with architectural characteristics that support evolution—modularity, configuration capabilities, API-first design, and integration readiness.
- Implement Incrementally: Follow a phased implementation approach that delivers value early while building toward more advanced capabilities.
- Prepare for Automation: Even if not immediately implementing automation, select systems that accommodate future automation adoption through appropriate integration capabilities.
- Balance Immediate and Future Needs: Make technology decisions that address current operational requirements while positioning for long-term evolution.
The competitive advantage of a flexible WMS
The speed of change in modern supply chains shows no signs of slowing down. As complexity continues to grow, so does the strategic value of a warehouse that can adapt quickly.
Flexible warehouse management solutions allow you to respond to market shifts—whether it’s a sudden spike in demand, a shift in order patterns, or an unexpected supply chain disruption—by scaling your operations and adopting new technologies without constant overhauls.
Having the freedom to incorporate innovation, refine processes, and make strategic pivots leads to continuous operational improvements. Over time, these enhancements can translate into stronger financial performance, higher customer satisfaction, and a clear edge over competitors.
In a world where tomorrow’s warehouse looks very different from today’s, organizations that invest in flexible, future-proof warehouse management technologies can navigate evolving requirements with ease, turning operational excellence into lasting market leadership.
Set the right foundation for MHE warehouse solutions
Need a structured map to simplify your growth journey? Whether you’re considering your first WMS, OMS, or looking to switch to a more flexible foundation, Deposco is your strategic advantage.
The platform behind 1.2% of total US ecommerce during Peak 2024, Deposco is supply chain’s GPS – directing immediate results while positioning businesses for long-term success with innovation.
Transform your warehouse from a cost center into a powerful strategic advantage for your business.