You’ve invested in cutting-edge AI systems for your supply chain; how can you ensure that the promised breakthroughs materialize? It’s all about getting your forecasting, your inventory management system, and your WMS telling the same story – with rich insights your executives can understand and use.
Today let’s discuss the importance of data unification, a top catalyst for your success with AI.
23% of supply chains have eliminated data fragmentation
Have you? Our new AI research report uncovered a startling reality: 78% of executives maintain separate systems for inventory, ordering, logistics, and planning. That means if you’re an early adopter of unified data, you gain a clear advantage because you no longer have disconnected systems and data silos, a fundamental ingredient for improving AI effectiveness.
Learn how to break down these silos and create the unified foundation essential for AI success. New AI report: “AI in Supply Chain: How Leaders are Driving Breakthrough ROI”.
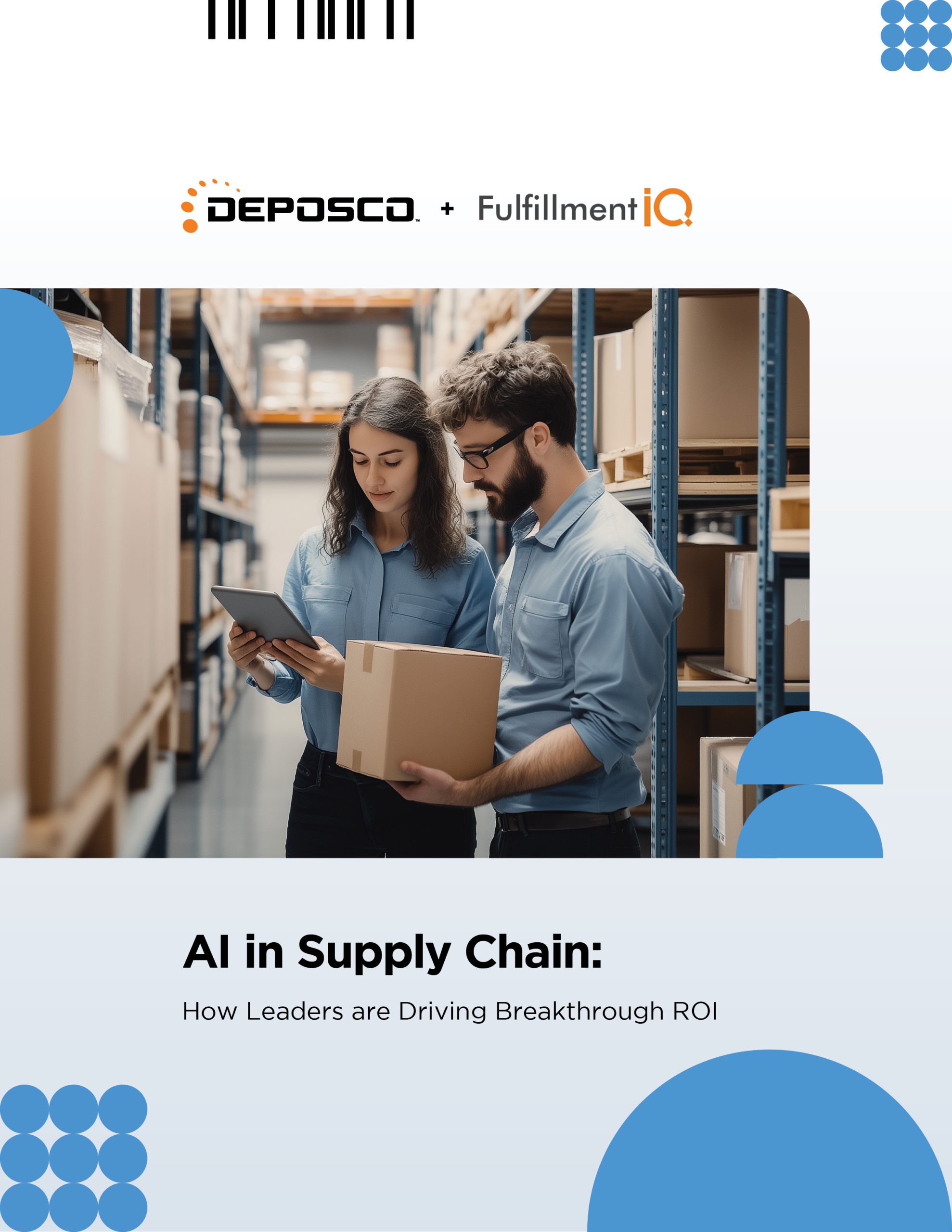
The high cost of data fragmentation
Think of AI as an engine. You can invest in the most powerful, technologically advanced engine in the world – but if you’re feeding it low-quality fuel, it’s never going to perform as designed.
In the AI world, data is that fuel. While your competitors rely on fragmented, inconsistent, or outdated data, it’s the equivalent of filling up a Ferrari’s gas tank with maple syrup. They will see results that are predictably disappointing.
Meanwhile, those 23% taking a unified data approach are achieving breakthrough results with AI. It’s not about who is using the most advanced algorithms – it’s simply integrating data foundations that span planning, execution, and analytics to see stronger ROI from your AI investment.
These aren’t incremental improvements – they’re transformative advantages that compound over time. Every percentage point of improved forecast accuracy cascades through your operation, reducing safety stock, minimizing expedited shipping, and improving customer satisfaction.
Integration matters more than algorithms
Siloed data doesn’t just introduce inconsistency – it’s that AI can only optimize what it can see. Your demand forecasting system can’t account for transportation constraints it doesn’t know about. Your inventory optimization algorithm can’t consider warehouse capacity limitations it doesn’t have access to.
This is why even the most advanced point solutions for supply chain management often fail to deliver their promised value. As Jason Franklin, Senior Director of Product Marketing at Deposco, puts it: “AI within point solutions is pointless. You can invest millions in separate AI tools for demand planning, warehouse optimization, and transportation—but if they can’t talk to each other, or operate from the most up-to-date or accurate data, you’ll be disappointed with the payoff.”
McKinsey’s research reinforces this reality: “Companies that outperform in supply chain operations don’t view AI as a series of isolated use cases. They build integrated data foundations and capabilities that span planning, execution, and analytics. This approach delivers 2-3 times greater ROI than disconnected point solutions.“
You don’t have to boil the ocean
Creating a unified data foundation for AI doesn’t mean you have to boil the ocean. The most successful organizations in our research took a pragmatic, phased approach:
First, they identified their most critical data domains – typically starting with inventory, orders, or product data. They focused on creating a single source of truth for these core entities before expanding to other areas.
Second, they implemented robust data governance processes to ensure ongoing data quality and consistency. This isn’t just a technical issue – it requires clear ownership, processes, and accountability across the organization.
Third, they chose platforms that natively integrate execution, intelligence, and planning capabilities rather than cobbling together disparate point solutions. This approach creates a virtuous cycle where clean execution data feeds intelligent insights, which then drive more effective planning.
As one survey respondent told us: “We spent years trying to force our disconnected systems to talk to each other through custom integrations. It was expensive, fragile, and ultimately futile. Moving to a unified supply chain platform with built-in intelligence was like night and day – suddenly our AI investments started delivering real value.”
46% of organizations are already achieving breakthrough ROI with AI systems fueling their supply chains.
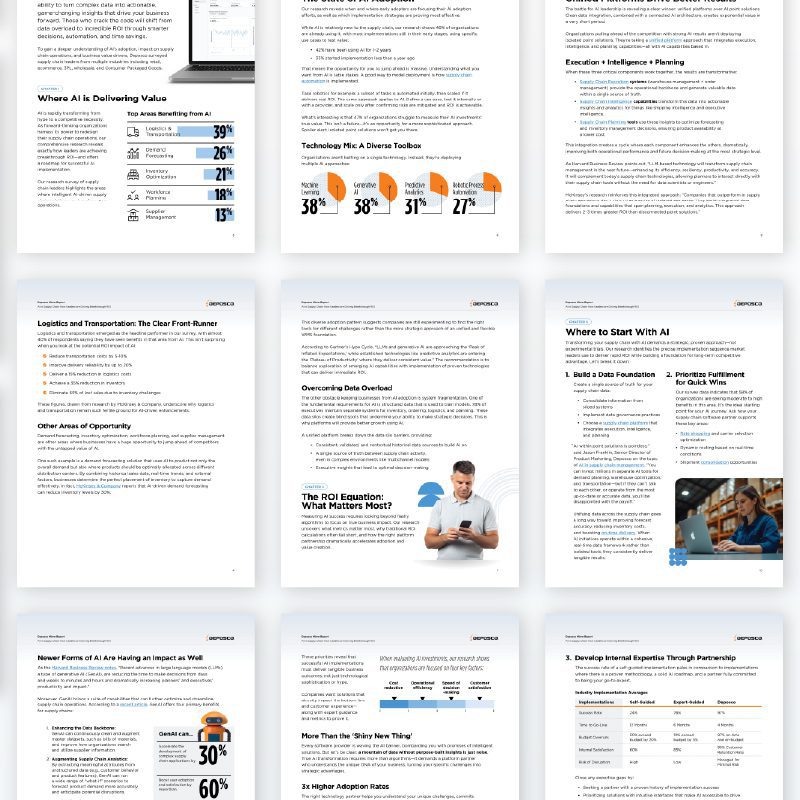
How to unify your AI systems for max ROI
The organizations seeing the greatest ROI from AI are building their strategies around three interconnected pillars:
- First, they establish robust execution systems (WMS software + OMS software) that provide the operational backbone and generate clean, consistent data. These systems aren’t just where work gets done – they’re the foundation for everything that follows.
- Second, they implement shipping and executive intelligence capabilities that transform this data into actionable insights. This is where AI truly shines – identifying patterns, predicting outcomes, and recommending actions that would be impossible for humans to discern from complex supply chain data.
- Third, they deploy planning solutions that use these insights to optimize future decisions, ensuring product availability at the lowest possible cost. This closes the loop, creating a virtuous cycle where execution generates data, intelligence creates insights, and planning improves execution.
The magic happens when these three components work together on a unified platform. Companies can start with high-impact use cases today while easily expanding to more sophisticated applications tomorrow.
The data quality imperative
Beyond AI system integration, successful implementations require a relentless focus on data quality. Our research found that 87% of IT and analytics leaders believe AI advancements have made high-quality data management a top priority. Yet 41% of organizations admit their data strategy isn’t aligned with business goals.
This disconnect explains why many AI initiatives fail to deliver expected results despite significant investments. You can’t expect strategic insights from tactical data, no matter how sophisticated your algorithms are.
Leading organizations approach data quality as a business initiative rather than an IT project. They establish clear ownership, implement robust validation processes, and continuously monitor data quality metrics. Most importantly, they recognize that data quality isn’t a one-time effort – it’s an ongoing commitment that requires sustained focus and solid change management resources.
Adnan Nathani, Director of Product Management at Deposco, reveals “The Human Side of AI” — a look inside how to balance technological advancement with robust risk assessment and responsible change management.
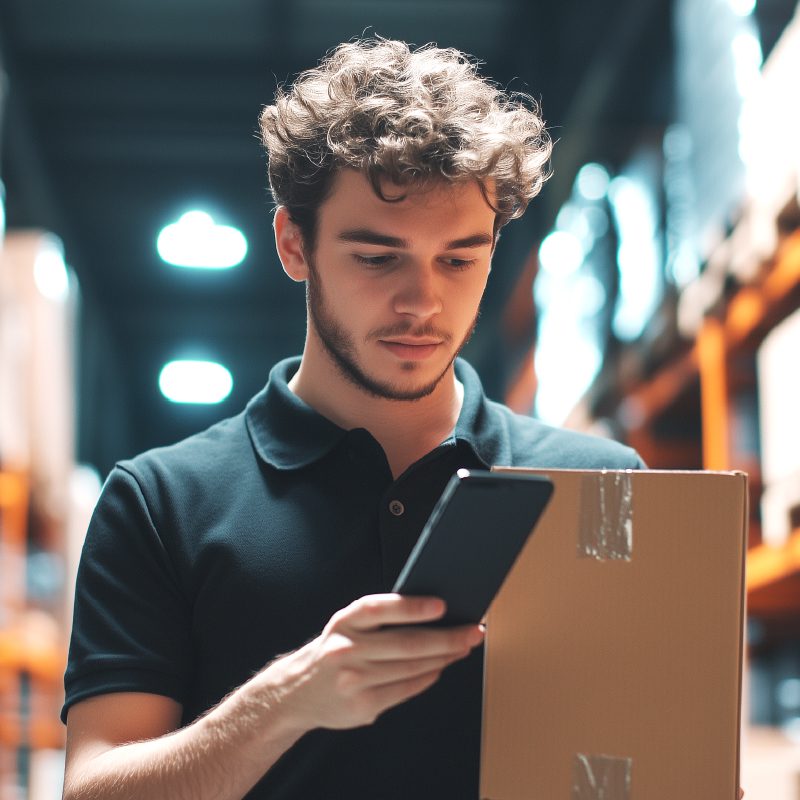
Your path forward
If you’re currently struggling with fragmented supply chain systems and inconsistent data, there’s a clear path forward:
Start by taking inventory of your current systems and data flows. Identify where inconsistencies and gaps are undermining your decision-making capabilities.
Then focus on creating a unified foundation for your highest-value processes. This doesn’t mean you need to rip and replace everything overnight – but it does require a strategic commitment to integration and data quality.
Most importantly, choose a supply chain software partner that understands the critical importance of unified data for AI success. Look for AI system platforms that natively integrate execution, intelligence, and planning capabilities rather than forcing you to stitch together disconnected point solutions.
The companies that get this right aren’t just improving efficiency – they’re fundamentally transforming how they operate. They’re making better decisions faster, allocating resources more effectively, and delivering superior customer experiences.